Diana Barnum, Correspondent Waste disposal problems can mount
quickly, with labor, handling and transporting coordination and payment,
landfill-tipping fees that seem to escalate and new material costs are
only some of the ongoing issues facing waste-handling companies
today.
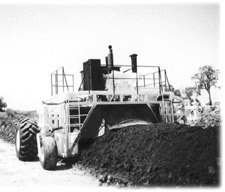
Grasan KRH1010 with truck.
But recycling construction and demolition (C&D) debris can turn
all of these problems into paying solutions with the right equipment. Two
such popular pieces are the KR1515 Impactor Crushing Plant and the KR1010
Compact Rubble Plant from Grasan of Mansfield, Ohio. “The KR1515,
Grasan’s largest road-portable primary impact crushing plant, can be
configured for concrete/asphalt recycling (side discharge) or crushing
limestone (end discharge), providing reduction ratios as great as 30-to-1
in closed circuit,” said Carl Emigh of Carl Richards Creative
Services. The KR1515 features the Hazemag APPH impact crusher with a
fully automatic, hydraulic cylinder system, providing increased crusher
capacity (up to 600 tph), smoother operation and more uniform
products. Crusher adjustments have been simplified; no tools are
needed. The crusher inlet is 45-inches high to handle larger sizes of
debris. A hydraulic moveable inlet base helps clear jams. And a hydraulic
inlet hood secured with wedge pins makes for easy opening and closing. A
grizzly bypass chute easily keeps or rejects undersize material. And
sideliners in the crusher have been reduced from seven to three
standardized shapes, reducing spare parts’ inventories. All
multi-blocks have been made interchangeable. The Grasan KR1515 is
available with diesel or electric power. It includes a skid-on, skid-off
hopper and six independent hydraulic support legs, easy set-up and
teardown operation. No crane required.
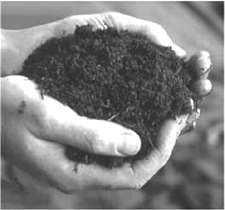
Grasan KRH1515 Impact Crusher Plant. Photos courtesy of
Grasan
Power is the name of the game and the KR1515 packs a wallop with its
ability to handle more than 500 tons of concrete per hour, yet leaving
steel completely clean. Cost-conscious clients say they can run up to 700
tph of limestone through the impactor, outdistancing a jaw by several
hundred tons per hour. “The Grasan KR1515 receives high marks for its
power and productivity,” said Norman Cole of Cole Consultants Inc. in
Cleveland, a heavy equipment engineer and private consultant to OEMs on
quarry and mining equipment. “It has earned a reputation for dependability
and low-maintenance needs.” The quick turnaround time for setup,
operation and teardown are notable Grasan features, with the ability to
move from one worksite to another and be up and operating in less than a
day. Another outstanding Grasan trademark is the company’s willingness
to customize its equipment. “Not a lot of manufacturers of quarry and
mining equipment want to be bothered with the time and expense in
accepting custom orders,” said Neil Pontagne, a retired equipment designer
and now a freelance writer for OEM publications. “Grasan does it and
customers appreciate their quality of design and the equipment’s
production capabilities. They just don’t put on a few bells and whistles;
their reputation is they provide quality innovations and designs and
really work closely with their customers to give them what they
want.” One piece of equipment that clients are snapping up is Grasan’s
KR1010 Compact Rubble Plant, is only 12’ 6” high, 8’ 6” wide, and 45’
long. Designed for small-to-medium size jobs in cramped urban areas, it
sets up in 15 minutes, processing concrete and asphalt debris at up to 150
tons per hour. It features the six-cylinder, 8.1-liter John Deere 6081A
diesel engine, developing 240 hp at 1800 rpm. An exhaust silencer quiets
the operation. A Hazemag APSE 1010/Q primary impactor crusher has a 25”
high by 40”-wide feed opening with hinged inlet hood, hinged split
housing, adjustable aprons and large access door. Easy access to crusher
and engine is available through the operator’s station and service
walkway. The vibrating grizzly feeder is a heavy-duty Seco 42” by 14’
with a direct-coupled 30 hp hydraulic motor for variable speed control.
Fine material can be removed by a bypass section or optional reject belt.
A 36” by 30’ with 8” discharge conveyor boasts a channel frame and tubular
cross members. For more information about turning C&D problems into
profits, contact Grasan, 440 South Illinois Avenue, Mansfield, Ohio
44907-1809. Call: (419) 526-4440, or fax inquiries to: (419) 524-2176.
E-mail inquiries to: grasan@grasan.com. |